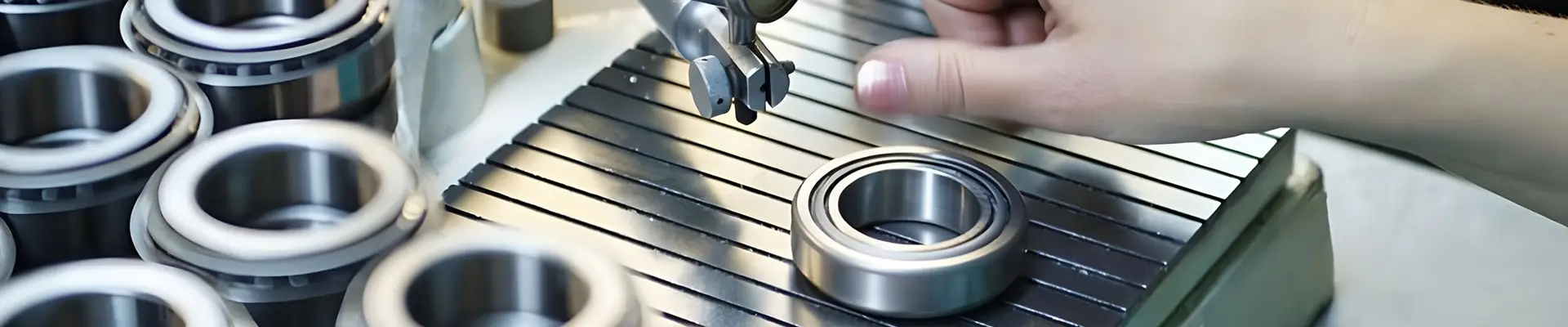
Maintaining Consistent Performance with Radial Ball Bearings in Electric Motors
Maintaining Consistent Performance with Radial Ball Bearings in Electric Motors
Table of Contents
- Understanding Radial Ball Bearings
- The Importance of Bearings in Electric Motors
- How Radial Ball Bearings Work
- Benefits of Using Radial Ball Bearings
- Choosing the Right Radial Ball Bearing
- Maintenance Tips for Radial Ball Bearings
- Common Issues and How to Avoid Them
- The Future of Radial Ball Bearings in Electric Motors
- Conclusion
- FAQs
Understanding Radial Ball Bearings
Radial ball bearings are one of the most commonly used types of bearings in machinery, particularly in electric motors. These components consist of balls that are held in a raceway, allowing for smooth rotation and reducing friction between moving parts. The primary function of radial ball bearings is to support radial loads, which are forces acting perpendicular to the shaft of the motor.
Components of Radial Ball Bearings
Radial ball bearings typically comprise the following components:
- **Inner Race**: The inner ring that fits onto the shaft.
- **Outer Race**: The ring that fits within the housing or casing.
- **Balls**: The rolling elements that reduce friction.
- **Cage**: The component that holds the balls in place and ensures even spacing.
The Importance of Bearings in Electric Motors
Bearings play a critical role in the functionality and efficiency of electric motors. They not only facilitate smooth motion but also contribute significantly to the overall performance and lifespan of the motor. Properly functioning bearings ensure that electric motors operate at optimal efficiency, reducing energy consumption and wear and tear.
Enhancing Motor Performance
Electric motors equipped with high-quality radial ball bearings experience reduced vibration and noise, contributing to a more stable and quieter operation. This enhancement in performance is crucial for applications where precision and reliability are paramount.
How Radial Ball Bearings Work
The operation of radial ball bearings is based on the principle of rolling friction. When the electric motor runs, the inner race rotates around the shaft while the balls roll within the races. This motion minimizes direct contact between the moving parts, significantly reducing friction and heat generation.
Load Distribution
Radial ball bearings are designed to carry loads effectively. They provide excellent load distribution capabilities, enabling them to handle both radial and axial loads, although they are primarily optimized for radial loads.
Benefits of Using Radial Ball Bearings
Utilizing radial ball bearings in electric motors offers several advantages:
- **Longevity**: High-quality bearings can significantly extend the lifespan of electric motors by minimizing wear and tear.
- **Energy Efficiency**: Reduced friction leads to lower energy consumption, which is essential for sustainable operations.
- **Versatility**: Radial ball bearings are versatile and can be used in various applications, from small appliances to large industrial machinery.
- **Cost-Effectiveness**: Investing in reliable bearings can reduce the overall maintenance costs associated with electric motors.
Choosing the Right Radial Ball Bearing
Selecting the appropriate radial ball bearing is crucial for ensuring the optimal performance of electric motors. Here are some factors to consider:
Load Ratings
Understanding the load ratings is essential. Bearings are rated for radial and axial loads, and choosing a bearing that can handle the necessary loads without exceeding its limits is critical.
Speed Ratings
Consider the maximum speed at which the motor will operate. Bearings have maximum speed ratings, and using one beyond this limit can lead to premature failure.
Environmental Conditions
The operating environment can significantly impact bearing performance. Factors such as temperature, humidity, and exposure to contaminants should be considered when selecting bearings. For example, sealed bearings may be preferable in dusty environments.
Material Selection
Bearing materials can influence performance. Common materials include steel, ceramic, and hybrid options, each offering unique benefits in terms of durability and heat resistance.
Maintenance Tips for Radial Ball Bearings
To maintain consistent performance, it is vital to implement a regular maintenance schedule for radial ball bearings in electric motors. Here are some effective maintenance practices:
Regular Inspection
Conduct routine inspections to check for signs of wear and damage. Look for discoloration, pitting, or unusual noise during operation.
Lubrication
Proper lubrication minimizes friction and heat generation. Ensure that the bearings are lubricated according to the manufacturer’s specifications. Using the right type of lubricant is also essential for optimal performance.
Temperature Monitoring
Keep an eye on the operating temperature of the motor. Excessive heat can indicate lubrication failure or bearing wear. Implementing temperature sensors can help monitor this effectively.
Alignment Check
Misalignment can lead to uneven wear and premature failure of bearings. Regularly check the alignment of the motor and bearings to ensure they are correctly positioned.
Common Issues and How to Avoid Them
Understanding common issues that may arise with radial ball bearings can help in their prevention:
Overheating
Overheating is often a result of inadequate lubrication or excessive speed. Ensure that bearings are regularly lubricated and not pushed beyond their speed ratings.
Contamination
Contaminants such as dust and moisture can severely impact bearing performance. Using sealed bearings can help prevent these issues.
Wear and Tear
Regular maintenance checks and addressing issues promptly can mitigate wear and tear, extending the lifespan of the bearings.
The Future of Radial Ball Bearings in Electric Motors
As technology continues to evolve, so does the design and manufacturing of radial ball bearings. Innovations such as smart bearings equipped with sensors for real-time monitoring are becoming increasingly common. These advancements will contribute to more efficient and reliable electric motors in the future.
Conclusion
Incorporating radial ball bearings in electric motors is essential for maintaining consistent performance and longevity. By understanding their function, benefits, and maintenance practices, we can ensure that electric motors operate at optimal efficiency. Selecting the right bearings, coupled with regular maintenance, can significantly enhance motor performance, reduce costs, and prolong lifespan.
FAQs
1. What are radial ball bearings used for?
Radial ball bearings are primarily used to support radial loads in rotating machinery, providing smooth operation and reducing friction.
2. How do I know if my radial ball bearings need replacement?
Signs of wear, such as unusual noises, excessive heat, and visible damage, indicate that it may be time to replace your bearings.
3. What type of lubrication is best for radial ball bearings?
The best type of lubrication depends on the application and environmental conditions. Typically, high-quality grease or oil specified by the manufacturer is recommended.
4. Can I use radial ball bearings in high-speed applications?
Yes, radial ball bearings can be used in high-speed applications, but it is crucial to choose bearings rated for the specific speed requirements.
5. How often should I inspect my radial ball bearings?
It is advisable to conduct inspections regularly, at least every few months, depending on the operational conditions and usage frequency.
Related News